Have you ever dreamed of building your own storage space, workshop, or even a comfortable home? Perhaps you’ve considered the versatility and cost-effectiveness of a pole barn. But what about the foundation? A concrete floor can significantly enhance the durability and utility of your pole barn, making it a worthwhile investment. This comprehensive guide outlines everything you need to know about building a pole barn with a concrete floor, from planning to pouring.
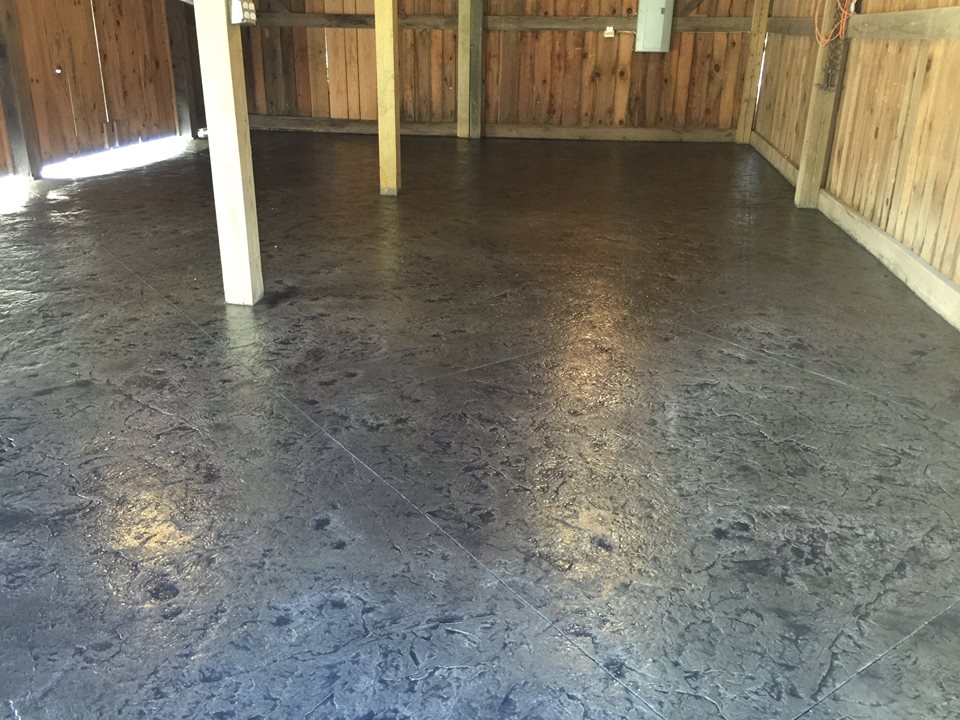
Image: www.blackwaterconcrete.com
Building a pole barn with a concrete floor is a great way to create a sturdy, durable, and attractive structure. A concrete floor offers various advantages, such as resistance to moisture, pests, and fire, durability, easy cleaning, and a smooth, level surface for various uses.
Planning Your Pole Barn with a Concrete Floor
1. Design and Planning
Before you start digging, you need a solid plan for your pole barn. This includes determining the size, purpose, and desired features of your structure. For example, if you’re building a workshop, you’ll need to consider the necessary work space, equipment, and potential for future expansion.
2. Site Preparation
The chosen site for your pole barn needs to be level and well-drained. Ensure that any obstacles like trees or existing structures are cleared, and that utility lines are marked and accounted for.

Image: www.buildingsbytimberline.com
3. Permit and Inspection Requirements
Depending on your location, obtaining the necessary building permits and inspections may be necessary. Check with your local building department about specific requirements for pole buildings and the concrete floor construction.
Foundation: Laying the Groundwork
1. Excavation
Once you have all the necessary permits, you can start excavating for the foundation. The depth of excavation will depend on local frost lines and the desired thickness of your concrete floor. It’s essential to excavate the area to a uniform depth and level for a solid foundation.
2. Compaction
After excavation, the soil must be compacted to prevent settling after the concrete is poured. A mechanical compactor is usually used for this task, achieving a firm and stable base.
3. Gravel Base
Before pouring the concrete, a layer of gravel is spread over the compacted soil. This gravel acts as drainage to prevent moisture buildup and helps provide a stable base for the concrete. The gravel layer typically ranges from 4 to 6 inches in depth.
4. Setting Up the Forms
Forms are essential to shape and contain the concrete. They are typically made from wood or metal panels joined to create a frame. They need to be secure, level, and strong enough to withstand the weight of the wet concrete. The forms should extend beyond the desired edge of the concrete floor to create a lip, allowing for easier finishing. This lip can be removed after the concrete has set.
Pouring and Finishing the Concrete Floor
1. Ordering and Delivering Concrete
You’ll need to order the concrete from a local supplier. The quantity of concrete required will depend on the size of your pole building and the desired thickness of the floor. Be sure to specify the type of concrete, including compressive strength and slump, which affect its workability.
2. Placing the Concrete
The placement of concrete involves carefully pouring the concrete into the forms and ensuring it reaches all corners of the designated area. It’s usually done with a concrete pump truck that delivers the concrete directly into the forms, or it can be placed manually by wheelbarrow or shovels.
3. Consolidating and Leveling
Once the concrete is placed, it needs to be consolidated to remove air bubbles and create a dense, even texture. A concrete vibrator is used to achieve this. Next, it needs to be leveled, ensuring a smooth and even surface. This is typically done with a long, flat tool called a screed, pulled across the concrete to level it against the forms.
4. Curing
Curing is the process of allowing concrete to gain strength and harden. This is usually done by covering the concrete with a damp cloth or plastic sheeting to keep it moist. It’s essential to keep the concrete moist for several days to prevent cracking and ensure proper hydration.
5. Finishing Touches
Once the concrete has set, you can add finishing touches to enhance the appearance and functionality of the floor. Depending on your needs, you may choose to apply a sealant to provide protection, add a decorative coating, or even add an epoxy finish to create a durable and seamless surface.
Key Considerations for Building a Concrete Floor
1. Choosing the Right Concrete
A crucial factor in creating a durable and functional concrete floor is selecting the right concrete mix. The type of concrete you choose should be suitable for the purpose of the pole barn – for example, if you’re building a garage or workshop, higher compressive strength might be needed.
2. Concrete Thickness
The appropriate thickness of your concrete floor should be chosen based on the intended use of the pole barn and local building codes. Thicker concrete provides better durability and resistance to cracking but also adds to the total cost.
3. Reinforcing the Concrete
For added strength, reinforcing steel mesh or rebar can be embedded within the concrete. This is particularly important for areas where the flooring will experience heavy loads or movement, such as those used for machinery or vehicles.
4. Expansion Joints
Expansion joints are gaps built into the concrete floor to accommodate movement caused by temperature fluctuations or shifts in the ground. This helps prevent cracking and damage to the floor.
5. Slope
Introducing a slight slope to the floor can help with drainage and prevent water from pooling. A slope of about 1/8 inch per foot is usually sufficient.
Advantages of Building a Pole Barn with a Concrete Floor
Building a pole barn with a concrete floor offers several advantages, making it an appealing option for a range of construction projects:
- Durability: Concrete floors are extremely durable and can withstand significant wear and tear, making them ideal for a variety of uses, from storage to workshops and garages.
- Moisture Resistance: Concrete is naturally resistant to moisture, making it a suitable choice for areas prone to dampness or where water leaks might occur. This is particularly beneficial for storage spaces, workshops, and livestock facilities.
- Pest Resistance: Concrete floors deter pests and insects, making it a healthier and more hygienic option compared to dirt or gravel floors.
- Fire Resistance: Concrete is a fire-resistant material, providing added safety and security for your pole building.
- Easy Cleaning: Concrete floors are easily cleaned and sanitized, making them ideal for workshops, garages, and areas where spills or dirt may occur.
- Level Surface: A concrete floor provides a smooth, level surface, ideal for equipment, machinery, and vehicles.
- Versatility: Concrete floors can be customized with various finishes and coatings, allowing you to tailor them to your specific needs and aesthetic preferences.
Cost Considerations for a Concrete Floor
The cost of building a concrete floor can vary depending on several factors, including the size of the floor, the type of concrete used, the thickness, and the complexity of the project. Factors like excavation costs, labor, material costs, and any additional features, like reinforcing steel, can also affect the overall cost.
Building A Pole Barn With Concrete Floor
Conclusion
Building a pole barn with a concrete floor is a smart and practical choice for those seeking a durable, versatile, and long-lasting structure. By following the guidance outlined in this article, you can create a solid foundation for your pole barn, maximizing its value and functionality.
Remember, planning and research play vital roles in successfully building your pole barn with a concrete floor. Always consult with local building codes and regulations for specific requirements. Don’t hesitate to seek professional guidance from experienced contractors or engineers to ensure your project is executed efficiently and with lasting results.